Das Extrudieren von Kunststoff
Neben dem Kunststoffspritzguss hat sich auch die sogenannte Extrusion von Kunststoff unter den Verfahrenstechniken fest etabliert. Beide Verfahren sind eng miteinander verwandt und nutzen die Formgebung als gemeinsames Prinzip zur Herstellung von Formteilen. Beim Spritzguss wird ein verflüssigter Kunststoff in eine Hohlform oder Kavität eingeleitet und dann per Andruck der zweiten Hohlform zu einem Körper gestaltet. Dagegen verarbeitet die Extrusion den verflüssigten Kunststoff, indem sie ihn durch eine formgebende Matrize zu einem Endlosprofil presst.
Beide Verfahren gehören demnach zu den urformenden Fertigungsverfahren nach DIN 8580, in der sie auch genauer beschrieben sind. Fachlich ausgedrückt stellt der Kunststoffspritzguss also ein zyklisches Verfahren dar, während das Extrudieren in einem Endlosprozess verläuft. Beide Verfahren dienen jedoch der Herstellung von definierten Werkstücken mit genau festgelegter Geometrie wie z.B. dem Querschnitt der Rohre und weiteren bestimmten Eigenschaften. Neben dem Urformen kommen bei der Kunststoffverarbeitung außerdem noch das Umformen und das Fügen zum Einsatz.
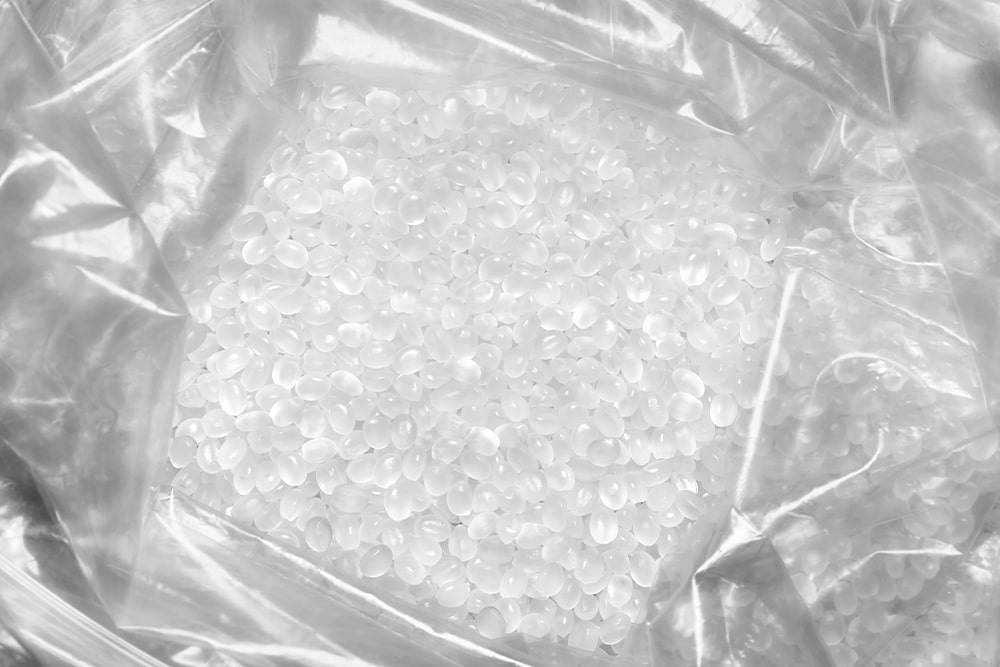
Wir planen und produzieren auch für Ihre Branche und Ihr Unternehmen.
Senden Sie uns Ihre Anfrage oder rufen Sie einfach an,
wir sind gerne für Sie da.
Prinzipien und Materialien für die Extrusion
Bei der Extrusion wird das sogenannte Extrudat erzeugt, in dem eine zähe, aber verformbare Masse durch eine genau berechnete Form gepresst wird und sich anschließend durch Abkühlung oder andere chemische Vorgänge verfestigt. Diese Öffnung wird je nach Teilverfahren und Maschinerie auch als Mundstück, Kalibrierung oder eben auch Matrize genannt. Theoretisch können bei diesem Prozess Querschnitte in beliebiger Länge hergestellt werden. Praktisch werden die Werkstücke jedoch nach dem Erreichen eines bestimmten Maßes quer zum Profil abgeschnitten und zur Weiterverarbeitung transportiert. Die bekanntesten Beispiele für extrudierte Kunststoff-Formen sind Rohre, Leitungen, Flaschen, Profile für Fenster, das Profil für Scheibenwischer, Schläuche oder z.B. auch Laufflächen für Autoreifen.
Das formgebende Prinzip der Herstellung ist so einfach, dass es bei entsprechender Ausrüstung auch für viele andere Materialien verwendet wird. Die Extrusion findet statt für
- Kunststoff, in der Hauptsache Thermoplasten
- Lebensmittel wie Teigwaren und Formfleisch
- Naturwerkstoffe wie Kautschuk
- Keramische Massen wie Ton oder Lehm (hier auch als Strangpressen bezeichnet)
- Verbundwerkstoffe aus Kunststoffen, Fasern und Zellstoffen
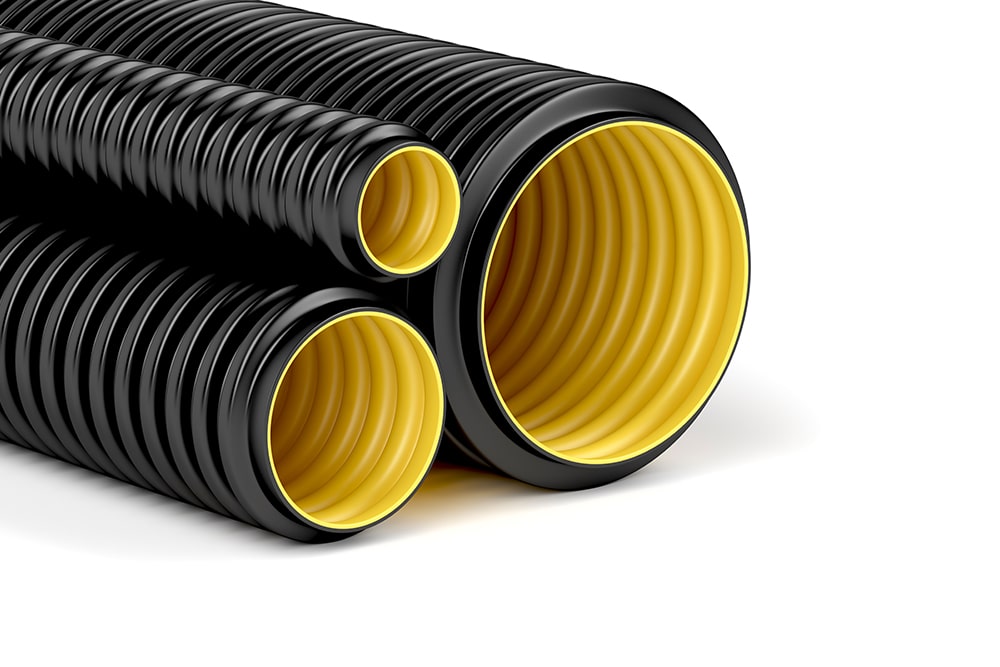
Eigenschaften wie bei Thermoplasten
Allen diesen Stoffen ist die thermoplastische Eigenschaft gemein, also die Verformbarkeit bei Hitze und die anschließende Erstarrung zu einer in Grenzen belastbaren Form. Je nach Material unterschiedlich ist jedoch sowohl die Temperatur als auch der Druck, der für die Extrusion mit dem Extruder aufgebracht werden muss. Die Bandbreite reicht vom Kaltpressen mit niedrigem Druck über das Warmpressen bis zum Heißpressen, jeweils mit unterschiedlich hohem Druck. Wenn durch die Extrusion verschiedene Stoffe vor dem Verlassen des Extruders durch das Mundstück zusammengemischt werden, spricht man auch von Koextrusion. Der verwendete Druck beim Extrudieren reicht von 10 bis 1.500 bar, die eingesetzten Temperaturen reichen von 30° bis 300° Grad Celsius.
Technik der Kunststoff-Extrusion
Ähnlich wie beim Spritzguss haben sich in der Extrusion seit seiner Erfindung schon im 19. Jahrhundert verschiedenen Arten des Verfahrens und verschiedene Konstruktionsformen der eingesetzten Maschinen entwickelt. Die einfachste Form des Extrudierens wird in der reinen Formgebung z.B. für thermoplastische Kunststoffe eingesetzt. Heute wird eine lange Reihe von Kunststoffen und Mischkunststoffen bei der Extrusion eingesetzt, um die gewünschten Profile zu erzeugen. Die Liste liest sich wie ein Querschnitt durch die bekanntesten Thermoplaste. Dazu gehören Polyvinylchlorid PVC, Polyethylen (PE), Polypropylen (PP) und Polyamid (PA), aber auch Polymethylmethacrylat (Acrylglas, PMMA), Polyurethan (PUR) oder das bekannte PET für die Getränkeflaschen.
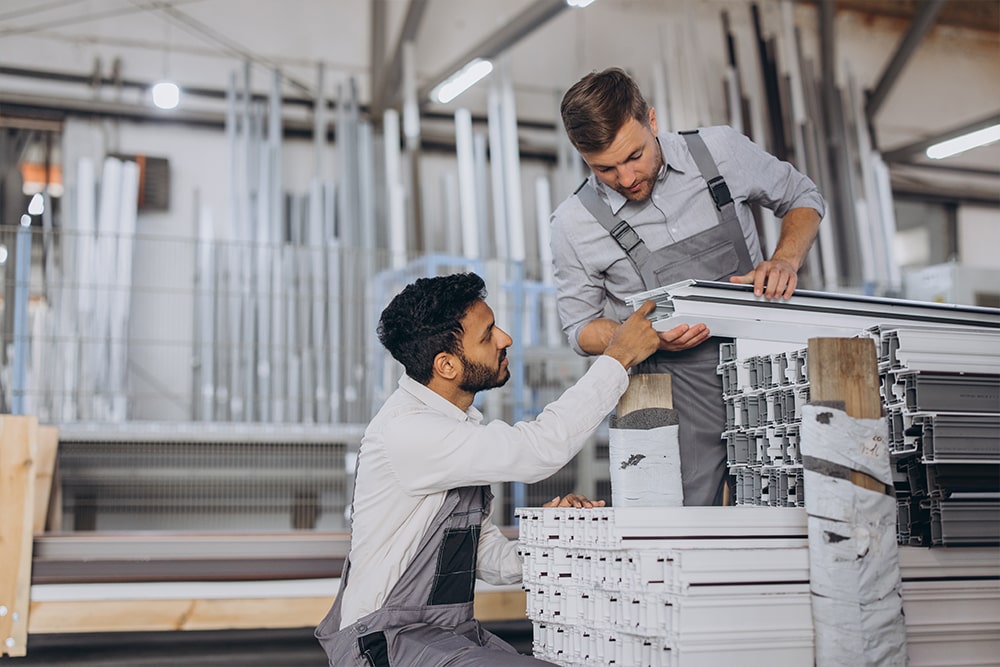
Verarbeitung oder Aufarbeitung
Das angelieferte Kunststoffgranulat wird während dieser Verarbeitungs-Extrusion durch Friktion in einem temperierten Schnecken- oder Kolbenextruder erhitzt und mit der Drehbewegung der einwelligen Schnecke oder dem Druck durch den Kolben zur Matrize geführt. Nach dem Austritt setzt die Erstarrung für das extrudierte Material ein. Dagegen werden die eingesetzten Kunststoffe oder andere Materialien im Aufbereitungs-Extruder während des Transports zur Matrizenform modifiziert. Diese Modifizierung kann durch Vermischung, chemische Reaktion oder auch durch Entgasung der Stoffe vorgenommen werden. Dann wird die einwellige Schnecke durch komplexe Knetmixer oder doppelwellige und gegenläufige Schnecken-Extruder ersetzt.
Der Schnecken-Extruder
Der Kolben-Extruder wird in der Kunststoff-Extrusion nur noch selten verwendet. Er eignet sich als eher grobes und stabiles Werkzeug besser für z.B. die Extrusion keramischer Massen. Der Schnecken-Extruder dient mit seiner Bauweise zunächst dem einfachen Transport, der Erhitzung und der Friktion der Kunststoffe vom Einfüllstutzen bis zum Mundstück bzw. der Matrize. Die Schnecke entspricht in ihrem Durchmesser nahezu den Maßen des Schneckenzylinders, in dem sie rotiert. Die Länge der Schnecke und damit die Dauer und Komplexität des Prozesses wird im multiplizierten Durchmesser angegeben, d.h. eine Schnecke mit 25D misst in der Länge das 25-fache ihres Durchmessers. Je nach Bauweise der Schnecke und des Zylinders können während des Transports der Thermoplasten zusätzliche Stoffe durch Ventile in den Seiten eingebracht werden. Bei dieser Seitenbeschickung werden z.B. Weichmacher, Farbstoffe und weitere Additive hinzugefügt. Die genau berechneten Komponenten, Dosierungen und Eigenschaften aller technischen Elemente erlauben teils sehr hohe Drehzahlen der Schnecken, die den Prozess der Extrusion z.B. auf 1.500 Umdrehungen in der Minute beschleunigen können.
Die drei Phasen im Schnecken-Extruder
Während der drei Phasen eines Schnecken-Durchlaufs wird das Material als Granulat zunächst erhitzt, aufgeschmolzen und transportiert, dann wird durch gesteigerte Friktion der Druck erhöht und schließlich in der dritten Phase der Ausstoß durch die Matrize bzw. Düse vorgenommen. Nach dem Verlassen der Matrize oder Düse beginnt ein weiterer nahezu eigenständiger Prozessabschnitt in der Extrusion. Das oft noch weiche und leicht verformbare Material für das Werkstück bzw. den Bereich des Querschnitts im jeweiligen Abschnitt muss jetzt in teils aufwendigen Verfahren in seiner Form gehalten werden. Diese sogenannte Kalibrierung kann in ihrer einfachsten Form durch Wasserkühlung hergestellt werden, indem das Werkstück eine Wegstrecke durch ein Wasserbad durchläuft.
Stabilität durch Vakuum
Für Rohre oder weit komplexere Formen wie die Profile für Fenster reicht aber aufgrund der bestehenden Hohlräume in der Form ein einfacher Andruck der Profile an die Wand der Kühlwanne nicht aus. Hier kann z.B. ein Kalibriertisch eingesetzt werden, der ähnlich einem Werkzeug beim Spritzguss genau den inneren Hohlraum des Rohrs nachbildet. Während das Rohr mit Raupenbändern über die Form geleitet wird, sorgt genau berechnete Stützluft oder auch ein Vakuum mit seinem Unterdruck dafür, dass das Werkstück die geplante Form beibehält und nicht nach innen kollabiert. Als weiteres Element der gesamten sogenannten Extrusionslinie gelangt das extrudierte Werkstück dann auf einen Schneidetisch, wo es auf die erforderlichen Längenmaße geschnitten wird. Danach erfolgt die Ablage auf dem Sammeltisch zum Abtransport der jetzt fertigen Bauteile, meist in Folien. Die Bezeichnung Extrusionslinie bringt dabei zum Ausdruck, dass sämtliche Elemente von Einfüllstutzen der Schnecke bis zum Sammeltisch hintereinander wie auf einer Linie angeordnet sind.