Spritzguss-Materialien aus Kunststoff
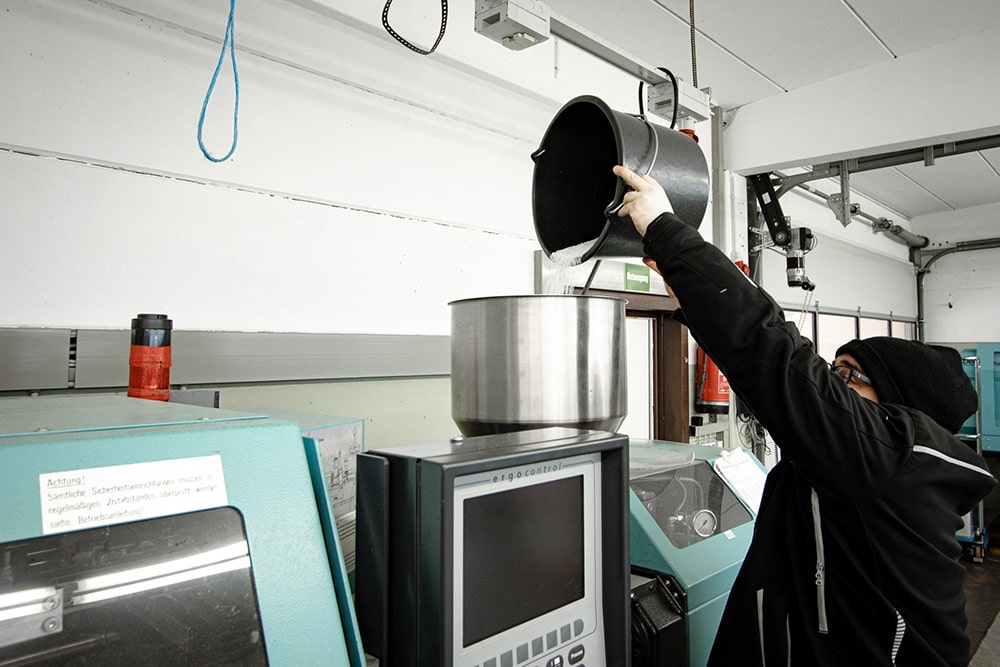
Das Spritzgießen hat sich ab ca. 1950 weltweit als Produktionsmethode für Kunststoffteile durchgesetzt. Es ist die wirtschaftlichste Methode, wie man in kurzer Zeit extrem viele Teile gleicher Bauart erzeugen kann. Die meisten der heute erzeugten Kunststoffe teilt man nach ihren Haupteigenschaften in drei Gruppen ein.
Thermoplaste verflüssigen sich beim Erreichen einer gewissen Temperatur und nehmen beim Abkühlen eine feste Form an. Dieser Vorgang lässt sich wiederholen. Duroplaste ändern ihre chemische Zusammensetzung, wenn man sie erhitzt. Die Form, die sie nach dem Abkühlen annehmen, kann beim erneuten Erhitzen nicht verändert werden. Bei einer gewissen Temperatur werden sie zerstört, erweisen sich bis dahin aber als sehr stabil. Elastomere haben die Eigenschaft, sich bei Raumtemperatur unter Druck oder Zug verformen zu lassen, um nach dem Ende der Krafteinwirkung wieder ihre ursprüngliche Form anzunehmen.
Wir planen und produzieren auch für Ihre Branche und Ihr Unternehmen.
Senden Sie uns Ihre Anfrage oder rufen Sie einfach an,
wir sind gerne für Sie da.
Spritzguss Materialien für das Spritzgießen
In den über 60 Jahren, die wir jetzt schon im Spritzguss in Untersteppach bei Edling tätig sind, hat sich in der Entwicklung der Kunststoffe viel getan. Es sind viele Tausend neue Kunststoffe und Mischungen entstanden, die alle ihre unterschiedlichen Fähigkeiten für den Spritzguss aufweisen und dementsprechend auch ihre Anwendungsgebiete gefunden haben. Allerdings sind die meisten für sehr spezielle technische Einsatzbereiche entwickelt worden. Viele Kunststoffe ähneln in ihren Eigenschaften bereits bekannten Verbindungen. So bleibt die Zahl der Materialien, mit denen wir spritzgießen, trotz aller neuen Entwicklungen überschaubar. Unternehmen im Spritzguss, die sich mit der Entwicklung neuer Kunststoffe beschäftigen, stellen die große Ausnahme dar. Diese Arbeit wird meist an den Universitäten geleistet. Allerdings finden sich auch einige sehr erfolgreiche Spezialisten, die als sozusagen Auftragsentwickler einen Kunststoff direkt für einen bestimmten Bedarf entwickeln. Über die Jahre hinweg lassen sich Tendenzen beobachten, die die Verteilung der Stoffe auf die verschiedenen Anwendungsbereiche betreffen. Dabei geht es immer um ein paar Faktoren, nach denen ein Kunststoff für seine technische und industrielle Verwertung ausgewählt wird.
Viele Kunststoffe kommen für den Spritzguss in Betracht
Es existieren diverse Datensammlungen, in denen die kommerziell verwertbaren Kunststoffe gelistet werden. Derzeit kommt man auf knapp 90.000 verschiedene Arten und Bezeichnungen! Diese ungeheure Zahl von Kunststoffen lässt sich in etwa 45 Polymer-Gruppen zusammenfassen, die sich wiederum in die beiden Hauptgruppen der Duroplaste und der Thermoplaste einteilen lassen. Dazu kommen die Elastomere, die wie der Naturkautschuk jedoch eher für zum Beispiel Reifen und Gummibänder verwendet werden. Die geschichtlich gesehen schon frühe Entwicklung der Duroplaste als erster Kunststoff hatte dazu geführt, dass sie in den ersten Jahren die Hauptgruppe für den Spritzguss bildete. Inzwischen haben sich jedoch die Möglichkeiten bei den Thermoplasten dermaßen erweitert, dass sie heute etwa 85% der kommerziellen Produktion ausmachen. Um Ihnen die grundsätzlichen Unterschiede der Duroplaste und Thermoplaste kurz in Erinnerung zu rufen: Die Duroplaste behalten nach ihrer Zusammenmischung und Aushärtung ihre einmal angenommene Form bei. Diese Aushärtung wird entweder durch chemische Katalysatoren oder durch große Hitze ausgelöst.
Die grundsätzlichen Bedingungen für die Auswahl des richtigen Kunststoffs
Die Auswahl des geeigneten Materials für Ihren Spritzguss verläuft natürlich üblicherweise nach den Eigenschaften, die das Spritzgussteil in seiner späteren Verwendung aufweisen soll. Dabei spielen folgende Eigenschaften mit, die genau bedacht werden wollen.
- Formbarkeit der Kunststoffteile nach dem Spritzguss
Soll das Gussteil auch nach der Herstellung noch bis zu einem gewissen Grad formbar sein? (Thermoplaste) - Elastizität beim Kunststoff
Inwieweit muss das Teil die originale Form wieder annehmen, wenn die Druck- oder Zugkräfte nachlassen? (Elastomere) - Härte des Kunststoffes
Wie soll das Material auf einwirkende Kräfte in unterschiedlichen Maßen reagieren? (Besonders hart: Duroplaste) - Bruchfestigkeit beim Kunststoff
Bis zu welchem Grad muss das Material den einwirkenden Kräften widerstehen, bevor es seinen Glasübergangspunkt überschreitet, also bricht? - Temperaturbeständigkeit beim Kunststoff
Welchen Temperaturen wird das fertige Bauteil ausgesetzt werden und wie lange muss es ihnen ohne Änderung seiner Eigenschaften standhalten? - Wärmeformbeständigkeit beim Kunststoff
Diese Untergruppe der Temperaturbeständigkeit konzentriert sich auf die Beibehaltung der Form unter hohen oder niedrigen Temperaturen. - Chemische Beständigkeit beim Kunststoff
Entscheidend ist bei vielen Einsätzen von Kunststoffen auch ihre Reaktion mit Säuren, Laugen, Ölen oder Salzen.
Bei all diesen Überlegungen kommt natürlich immer noch ein weiterer gewichtiger Punkt zum Tragen. Jede Kunststoffherstellung hat ihren Preis. Je seltener der ein
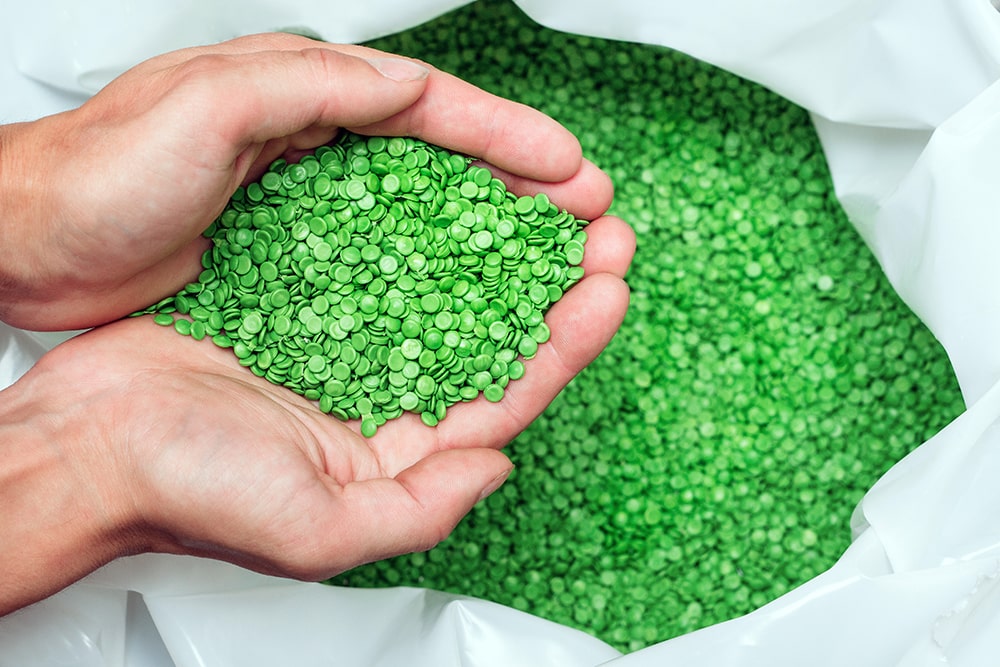
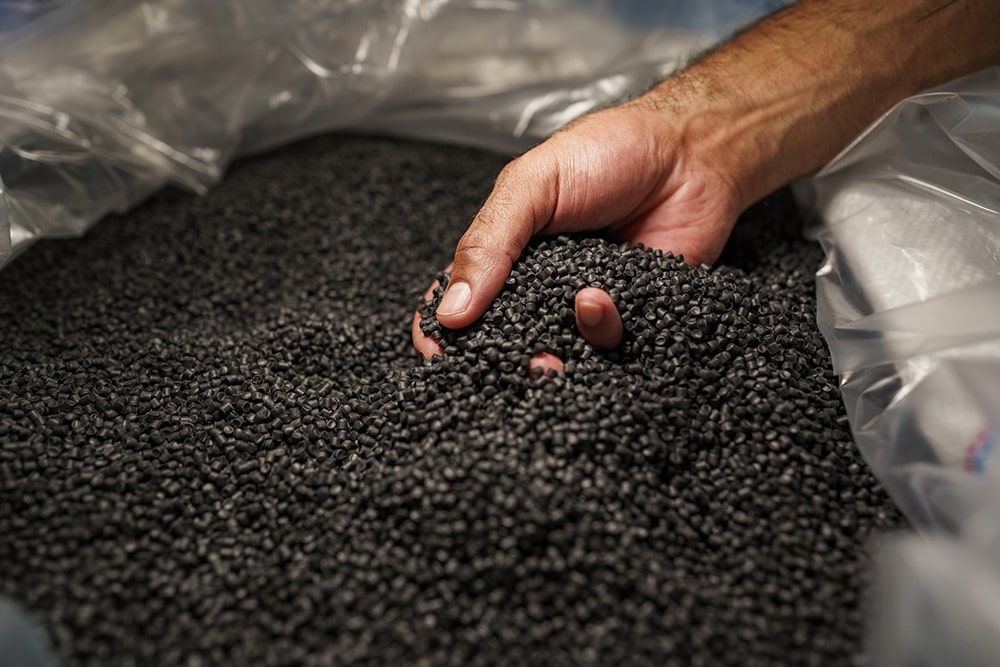
Thermoplaste wie PP, PE, ABS und PS bilden die Mehrheit
Es versteht sich, dass die Thermoplaste beim Spritzguss wesentlich mehr Spielraum für die Produktion liefern, wenn man ihre Eigenschaft in Betracht zieht, dass das Material sich beliebig oft wieder einschmelzen lässt und beim Abkühlen eine neue Form annehmen kann. Außerdem sind die Thermoplaste als Material nach dem Spritzguss schweißbar. Aber lassen wir die Vielfalt einfach mal beiseite. In harten Zahlen beschränkt sich das Spritzgießen von Kunststoff auf der Welt in der Hauptsache auf vier Materialien.
Knapp die Hälfte aller Spritzgussteile, die jedes Jahr hergestellt werden setzt sich aus Polypropylen (40%), Acrylnitril-Butadien-Styrol (30%), Polyethylen (15%) und Polystrol (10%) zusammen. Acrylnitril-Butadien-Styrol ist vielen unter dem Kürzel ABS bekannt. Aufgrund ihrer hohen Stabilität gegen Druck und Zug, der Fähigkeit, sich elektrostatisch nicht aufzuladen und ihrer hohen Feuerfestigkeit werden die Untergruppen ABS-ESD und ABS-FR hauptsächlich in der Herstellung für die Automobil- und Elektroindustrie verwendet.